Goat Tech
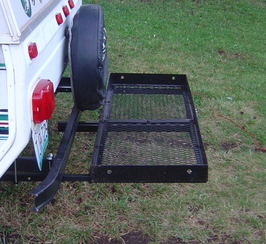
I made a tray to put on the back of my camper, to add some room for coolers and stuff when we go camping. It was kind of a fun project, and it turned out pretty well.
I used one of those receiver hitch trays for the back of an SUV and welded sections of square steel tubing on each end of it, width-matched to the frame rails on the camper. Another set of similar mounts are on the camper's frame rails, but they are clamped instead of welded.
Between those mounts are two sections of smaller square tubing that telescopes inside the larger stuff. This allows the tray's position to be adjusted, as well as making the tray attachable to the SUV and the camper (although not at the same time). The telescoping tubes, once adjusted, are held in place by pins.
Construction
I took the tray and the tubing to my brother's farm, and went to work. He has a chop saw, blowtorches, a drill press, a MIG welder, and all kinds of other stuff which makes this kind of work pretty quick. [About the welding I mentioned earlier: I didn't actually do it. My total lack of welding ability brought my progress to a halt before too long. Fortunately, my brother showed up and graciously offered to weld the tubes on the tray for me. He did a good job.]
I cut and drilled 8 small plates from 1/4" flat stock to make some big clamps. They look cool and hold the whole assembly on the camper with monster-truck force.
I actually did do some welding myself. I welded some plates on top of the front mounts to help position them on the frame. I wish now that I would have videotaped that process. It would have been hilarious to watch. I was wearing a t-shirt, tennis shoes, and shorts. I took a couple of hits from hot slag, and hopped around.
I lack a certain... competence in welding. It's hard to do. A MIG welder, unlike a stick welder, doesn't involve a disposable welding rod that arcs as soon as you touch the work. It feeds a fine copper wire through a small nozzle called a "contact tip", then through a cloud of argon gas, onto the work, when you pull a trigger.
So what happens is that you touch the work with the wire, get ready, pull the visor down on the welding helmet, and pull the trigger. That's when it arcs. Instantly, the wire vaporizes, and you're suddenly wrestling a small electric eel that's crapping molten metal onto your feet. You need to be precise and move the tip in some kind of deliberate fashion, but it's kind of hard to in all the confusion and pain. I ended up welding the tip of the welder to the piece I was welding, then welded the contact tip shut. I also welded the vise grip to the piece that I was welding, but the quality of the weld was so poor that I was able to break it off. Finally, I got a little better feel for the process, and actually welded my pieces together. Badly. It's a good thing no one's life or property depends on the integrity of these welds.
Some agressive work with a grinder made the welds look a little less like a pile of metallic vomit, and after I painted the pieces, they looked pretty good. I put the whole thing together this evening. I tested it by jumping up and down on it, and it seemed to hold up pretty well.
So I guess I now need to load it with something and go camping.
0 Comments:
Post a Comment
Subscribe to Post Comments [Atom]
<< Home